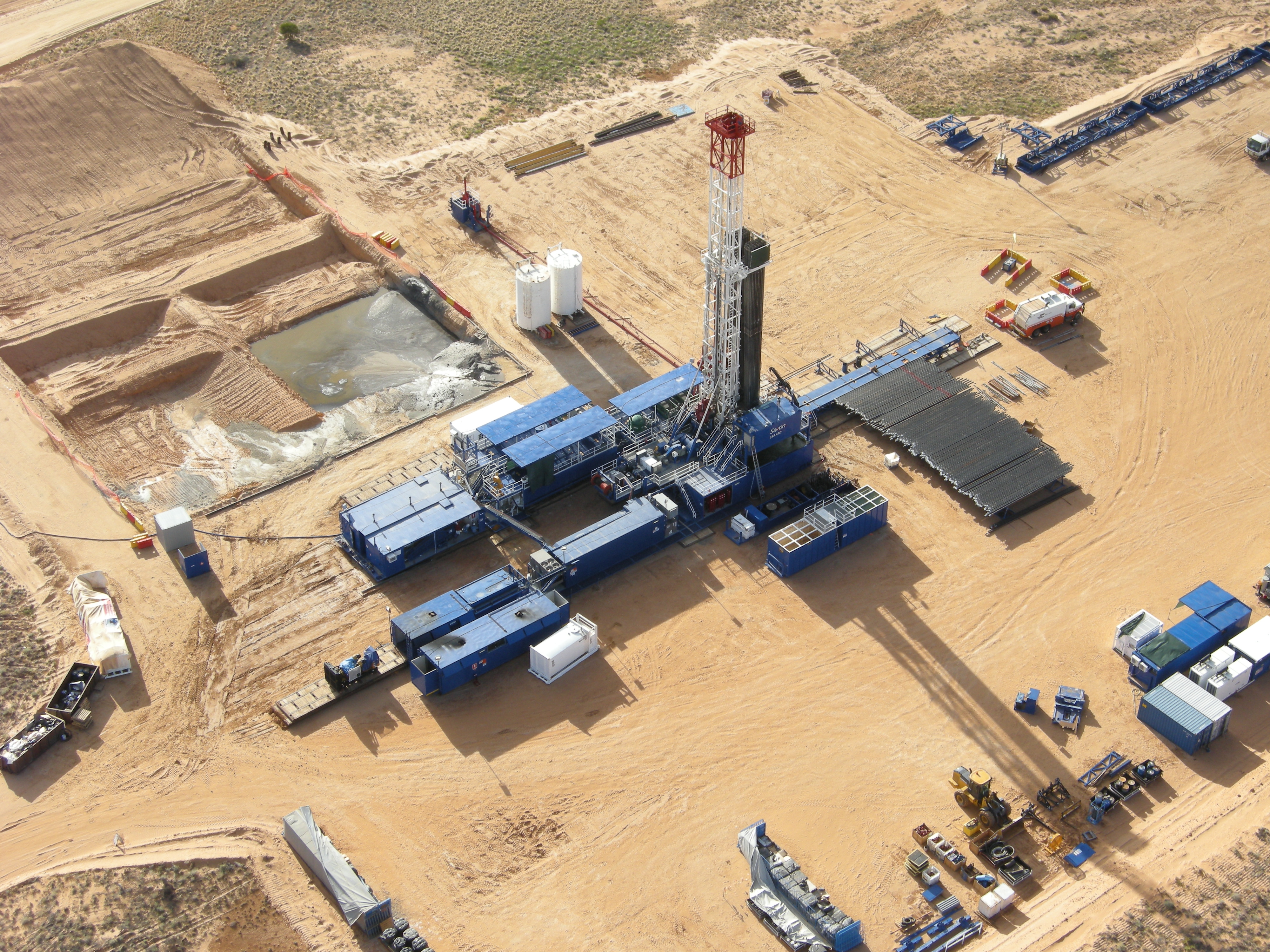
Founded in 2005 in Canada by a group of experienced drilling rig experts, Saxon Energy Services is now majority owned by oilfield services specialist Schlumberger and the largest private equity provider in the business, First Reserve.
Saxon started life in Ecuador, supplying just nine rigs there; since then, ithas transformed itself into a genuinely international drilling company with a fleet of about 100 rigs and a workforce of nearly 3,000 working in 13 countries. It came into this market on the back of the need in Australia to modernise and increase the number of the available rig fleet in country, and the expansion into the coal seam gas (CSG) market, says country manager for Australia, Daniel Marcano, a Venezuelan formerly responsible for the operation of Schlumberger’s rig operations in his native country and throughout Latin America.
The CSG industry has expanded dramatically over the last decade and is likely to continue to expand as demand in the domestic and export markets increases. CSG has attracted a lot of commercial interest because of its purity and non-toxicity. Historically, the gas was aired out as it was the cause of many mining explosions; however following increased global awareness of CSG capability as a viable energy resource in its own right as well as the development of more efficient technology for its extraction, the commercial utility of CSG is now being fully exploited.
The Saxon mantra is ‘Fit For Project’, and its latest Advanced Technology rigs, the ATD (Advance Technology Double) and ATS (Advance Technology Single) were found ideal for the conditions found in the Cooper Basin and the Queensland coalfields. Nevertheless this is a competitive market, and even these advanced technologies are widely available. What makes Saxon different from its competition, says Marcano, is the way it takes the burden from its clients, not only in terms of designing the right rigs for the job, but meeting the local regulatory constraints and above all the required safety standards to operate in Australia. “The key to delivering Fit For Project solutions is to adapt the rig itself, and all the different components around the central package to provide something that is suited to the type of wells that have to be drilled, the characteristics of the field in terms of rig moving, and the specifics of whether you want to drill several wells from the same location (on the same pad) or not.”
Many companies, he adds, will provide an off-the-shelf type of rig—from China or Europe perhaps—but without adding Saxon’s capacity for customisation for the specific task to be perfromed. Saxon’s rigs are built in the US or Canada; and during 2012 alone, Saxon will have brought into Australia equipment with a total value of more than $100 million—not the cheapest, but in terms of delivering value to the client by far the most cost effective way to conduct a drilling programme.
Last year Saxon brought in three sophisticated ATD rigs to drill 9,800-foot gas wells for Santos, which has been providing Australia with natural gas from the remote outback for more than 40 years, and today is one of the largest producers of natural gas for the Australian domestic market. The rigs operating in the remote Cooper Basin incorporate energy efficient AC-VFD (variable frequency drive) technology and a good deal of automation as well, says Marcano. “The automation is there to reduce the amount of manual interaction between the rig crews and the elements of the drill string. We try to eliminate manual work as much as possible to minimise the need for large crews, and the consequent potential exposure to hazards and incidents. For Santos, safety is a very high priority, and that’s another main reason why it wanted to invest in rigs that have a certain level of automation.”
The rigs are designed to be moved from one well to another using the available oilfield winch trucks and without the need to bring in cranes. At a single stroke, the cost of moving the rigs from well to well in this inaccessible part of Australia is reduced, the proportion of productive drilling is increased, and the risk of personal injury while disassembling and reassembling the rigs is brought down.
The biggest single contract to date is to provide nine rigs for Queensland Gas Corporation (QGC), a division of BG. These rigs are five completion rigs and four ATS 150 rigs designed for shallow depths that are being introduced in Australia and that the company hopes will bring about a step change in rig design for the shallow CSG drilling market. Three of these rigs are already working on the Bowen Basin coalfield in Eastern Queensland, he says, as a key part of QGC’s LNG project which will take the gas through a 540 kilometre pipeline to a natural gas liquefaction plant now under construction on Curtis Island, near Gladstone.
Once again, mobility is an important design element. The ATS rigs for QGC are trailer mounted and therefore very highly mobile, with remote monitoring, advanced instrumentation for data acquisition, and a pipe-handling system designed to reduce crew contact and promote safety and efficiency throughout the operation, explains Marcano. “Rig mobility is a key element of this operation. The focus on these rigs is to make them as light as possible and also to meet the Queensland road regulations, so they can be moved freely on the public roads without causing disturbances to the local communities. The wells that QGC needs to drill are comparatively shallow and short, so the time between wells becomes an important factor. If you take three days to drill a well then three days to move it, most of the time is spent moving not drilling. The rig design maximises the drilling time by averaging less than a day-and-a-half between wells.”
Another measure of Saxon Australia’s success is its headcount. From 100 employees at the beginning of 2012, the figure will rise to more than 450 by the end of the year. “We came to Australia with the primary objective of eventually using it as a foothold for expansion into Asia. However, at this moment, our primary focus is to address any and every opportunity to bring Fit For Project equipment into long-term CSG projects here in Australia. The main goal for the year 2012 is to get our initial contracts started in a safe and efficient way: we are bringing 13 rigs into the country, of which six are already here and three are already working; and we still have seven more to come.
“It’s quite a challenge for the organisation to support an operation of this size, and also a challenge to find enough skilled people to operate these rigs because the boom in the Australian industry is putting a real strain on available resources,” Marcano concludes.
Written by John O’Hanlon; research by Jeff Abbott
DOWNLOAD
SaxonEnergy-EMEA-July12-Bro-s.pdf